AV Design Engineering vs. Project Engineering
Project vs. Design Engineering
When I first joined the AV industry almost 20 years ago, I worked as a project manager for a small integrator in Baltimore. My understanding of AV engineering at that time could be summarized as “there are real engineers (those that worked for my company) and then there are consultants and designers”. The rationale for this skewed perspective was simple: consultants and designers handed us (the integrator) a design full of holes and assumptions, and it was our job to fix those “mistakes” and turn the project into a real-life system that a real-life person could use and benefit from.
Of course, this naïve and incorrect view was the result of being on only one side of the fence. In the following years, I have been lucky enough to serve in several different roles throughout the industry, from design engineer at a major university, to project engineer, to consultant. Each of these roles has presented different sets of challenges, but more importantly, they have allowed me to see the industry from both sides of the fence, and how each of these roles complement each other to produce satisfactory results for clients and end users.
So what are the actual differences between the “project” engineering and “design” engineering roles? From a distance, these can appear to be two descriptions of the same task, but as we’ll see the differences are significant, beneficial, and necessary for the success of larger-scale projects.
Definitions
For the purposes of this post, we’ll divide the engineering roles into two categories: Project Engineering and Design Engineering. Project Engineering is typically undertaken by one or multiple engineers working for or on behalf of an AV Integrator to produce construction drawings to be used by installers working for that integrator. Design Engineering, on the other hand, is typically undertaken by an independent consultant or pre-sales engineer, creating conceptual drawings which will typically be used by an integrator to create construction drawings.
Goals
As previously stated, an AV Project Engineer is producing construction-level drawings which will actually be used by technicians to install a system. This entails a much higher level of detail and specificity than expected in design-level drawings. As products are being purchased and labor hours are being spent based on the information contained in the drawing package, money is on the line. Every connector, cable, adaptor, and piece of mounting hardware must be accounted for and documented. Cable pull sheets can be generated from these drawings, so cables must be identified and labeled in an understandable scheme. The financial (and technical) success of the installation and project are often reliant upon the accuracy of these drawings. For example, if a Project Engineer overlooks the need for HDMI extension for a long cable run, an extender set may need to be ordered from the field, which can lead to project delays and significant cost impacts.
By contrast, the AV Design Engineer is responsible for creating a design set of conceptual drawings which reflect the project goals set forth by the end user. These conceptual drawings will then be interpreted by the Project Engineer to create the construction drawings. The Design Engineer is expected to have a much closer relationship with the end user, to ensure that the project goals are met, while considering any constraints (budget, timeline, aesthetics) identified by the end user.
Time and Money
Why then do we need to have design drawings at all? Why can’t the Project Engineer simply take the end user’s goals and design the system to construction level all by themselves without the need for a Design Engineer?
As with many things in business and life, the answer comes down to time and money. A Design Engineer is typically contracted directly to the end user or architect via a design contract. This happens very early in the development process, before contractors have been hired. The design team then has the time to meet with the client and stakeholders well before “boots are on the ground”. Budgets can be established, designs can be iterated and reiterated (and re-reiterated) with minimal impact on the overall project budget. Put simply, it is easy and relatively cost-free to make design changes on paper. Changes on-site are a different matter altogether.
Once construction contracts have been issued, boots are on the ground, and drywall is being hung, changes to the design of a system can have massive cost implications. Most integrators do not have engineers on staff that they can commit to being part of a multi-month or multi-year design process. Once they have been hired, they are on the clock to finish the project with (hopefully) a bit of profit in their pockets.
Relationships
An often-overlooked aspect of the importance of the division of the design and project engineering roles is that of impartiality and bias in relationships. While it can be expected that, as professionals, both Project and Design Engineers should value the relationship with the client equally highly as their bottom line, the same expectation might not always be true when it comes to product selection.
AV integrators, by their nature, must have relationships with the manufacturers of products that they sell and install. To ensure competitive pricing, on-time delivery, and pre- and post-sale support, integrators must cultivate and maintain these manufacturer relationships. Through no fault of their own, this means that integrators will tend to want to sell products provided by manufacturers with which they have good relationships.
While this is all well and good for the integrator, the needs of the project and end user may dictate equipment made by other manufacturers. This is where the value of independent Design Engineers and Consultants is made known. Rather than relying on the product offerings of a few select manufacturers, the independent Design Engineer can select the proper product for the application, regardless of the manufacturer.
Conclusion
While I wish I could go back and tell my younger self these important distinctions, the truth is that it took living and working in both the design and project engineering roles to truly appreciate the differences, as well as the necessity of both roles in the industry. Successful deployments of large-scale AV projects require both the design and project engineer specializations, and we should all be thankful for that!
Interested in more design or engineering related content? Check out “Revisiting ADA Mounting Requirements“.
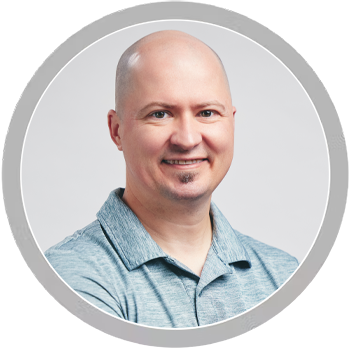
About the Author
John Rossman | CTS
BDM II – Technical Specialist
Supported Manufacturers: Harman Professional – AKG, AMX, BSS, Crown, DBX, JBL, Lexicon, Martin, & Soundcraft